Пищевая промышленность, в которую в качестве подотрасли входит консервная промышленность, является одной из важнейших отраслей страны.
Эффективность консервного производства при больших производительностях технологических линий, перерабатывающих сельскохозяйственное сырье, поточно-массовом характере процессов и жестких требованиях к качеству готовой продукции возможна лишь при условии четкой и слаженной работы всех звеньев производства, что выполнимо только на базе комплексной автоматизации производственных процессов. Создание автоматизированных систем управления консервными производствами требует применения различных технических средств автоматизации и вычислительной техники.
Для стерилизации (пастеризации) консервов применяют аппараты периодического или непрерывного действия. К аппаратам периодического действия относятся открытые ванны и автоклавы. Автоклавы представляют собой закрытые аппараты. Они бывают двух типов — вертикальные и горизонтальные. Наибольшее распространение в консервной промышленности получили вертикальные автоклавы, так как в них можно стерилизовать (пастеризовать) все виды консервов в жестяной и стеклянной таре.
Задачей автоматизированной системы управления автоклавом является управление, прежде всего двумя основными параметрами процесса автоклавирования: температурой и давлением. Предлагаемая в статье система предназначена для автоматизированного контроля и управления процессом водяной стерилизации (пастеризации) консервов, осуществляемым в автоклавах. Она представляет собой автоматизированное рабочее место (АРМ) оператора (технолога) технологического процесса стерилизации (пастеризации) консервов, производящегося на комплексе из одного либо нескольких автоклавов. Система функционирует на всех стадиях процесса стерилизации (пастеризации) консервов: заполнение автоклава водой, подогрев воды, загрузка автоклава корзинами, подъем температуры и давления до значений установленных формулой стерилизации (пастеризации), собственно стерилизация (пастеризация) и охлаждение консервов.
Задачи, решаемые при внедрении системы автоматического управления автоклавом:
- увеличение ресурса автоклавной установки за счет точного соблюдения технологического режима работы;
- обеспечение качества технологического процесса за счет точного поддержания необходимого температурного режима при прогреве обрабатываемых изделий;
- обеспечение безопасности работы установки путем реализации автоматических защит и блокировок;
- экономия энергоресурсов за счет оптимизации технологического режима и точного соблюдения алгоритмов работы;
- сокращение расходов на ремонты благодаря получению адекватных данных, обеспечивающих планирование техобслуживания и ремонта;
- снижение трудоёмкости обслуживания и улучшение качества документации путём автоматизации документооборота.
Современные промышленные автоклавы являются довольно сложными агрегатами с большой производительностью. Существуют специализированные модели автоклавов, но принцип их работы един и состоит в нагреве стерилизуемого (пастеризуемого) продукта (который, как правило, расфасован в стеклянную или жестяную тару) до высоких температур под давлением. Повышенное по сравнению с атмосферным давление в автоклаве компенсирует температурное расширение нагреваемого продукта и предотвращает разрушение тары, в которую тот упакован. Величина давления рассчитывается по так называемой формуле автоклавирования и зависит от значений температуры стерилизации (пастеризации) и прочих факторов (вид расфасовки продукта, коэффициент температурного расширения продукта и т.д.).
Внешний вид с разрезом автоклава марки Б6-КА2-В-2 приведён на рисунке 1.
1 – опора;
2 – корпус;
3 – теплоизоляция;
4 – крышка;
5 – кронштейны;
6 – патрубок;
7 – сливной патрубок;
8 – противовес;
9 – фланцевый затвор;
10 – автоклавные корзины;
11 – рассеиватель;
12 – подача сжатого воздуха;
13 – слив сверху;
14 – подача холодной воды;
15 –предохранительный клапан;
16 – коробка;
17 – место подключения датчиков;
18 – барботер.
В состав автоклава входят следующие основные части и компоненты: корпус, блок арматуры, средства механизации, теплоизоляция. Корпус 2 автоклава, предназначен для размещения корзин с консервами при проведении процесса стерилизации (пастеризации), представляет собой сварной цилиндрический сосуд с эллиптическим днищем, закрываемый сверху эллиптической крышкой 4. Корпус и крышка снаружи могут быть снабжены теплоизоляцией 3. Соединение крышки с корпусом осуществляется фланцевым затвором 9. Для уплотнения автоклава в плоскости разъёма к корпусу приварен фланец, а к крышке – фланец, в канавку которого установлено резиновое кольцо. К корпусу приварены три опоры 1 для монтажа автоклава, и четыре ребра для строповки. К корпусу автоклава приварена коробка 16, нижняя часть которой соединена с внутренней плоскостью автоклава, предназначенной для установки датчиков. Внутри корпуса в нижней части приварены кронштейны 5, для установки на них корзин установлен перфорированный кольцевой барботер 18, соединяемый с патрубком 6. К днищу корпуса также приварен сливной патрубок 7, над которым установлена сетка, предотвращающая попадание в магистраль слива инородных предметов. К крышке 4 приварены кронштейны для шарнирного соединения с корпусом, рычаги для противовесов 8, ручка для открывания и закрывания крышки.
Фланцевый затвор 9 включает в себя разжимное кольцо, состоящее из незамкнутого кольцевого пружинного пояса, секторов, рукоятки, пальцев, рычажной системы и деталей защиты.
Блоки арматуры предназначены для подключения автоклава к магистралям и обеспечивают: подачу пара, подачу воды, подачу сжатого воздуха, верхний и нижний слив воды. На подводящих магистралях блоки арматуры для пара, воды и сжатого воздуха собираются из мембранных исполнительных механизмов (МИМ). На магистралях слива блоки арматуры собираются из МИМов и запорных вентилей (ВЗ).
На некоторых предприятиях и в настоящее время можно встретить стерилизацию (пастеризацию) консервов при ручном управлении в водяной среде с противодавлением. Принцип работы такой стерилизации (пастеризации) основан на воздействии высокой температуры стерилизации и выдержке её в течение определённого времени. Контроль за технологическим процессом при этом осуществляется визуально с помощью прямого показания манометров и термометров. Не секрет, что при такой стерилизации (пастеризации) возможно влияние на ход технологического процесса человеческого фактора, что приводит к значительному браку готовой продукции и неизбежным финансовым потерям предприятия.
Предлагаемая в данной статье система автоматизации автоклава способна исключить влияние на технологический процесс стерилизации (пастеризации) консервов человеческого фактора и выполнять следующий функции:
- централизованный сбор данных о ходе процесса и состоянии автоклавов;
- отображение обобщенной (номер варки, ФИО оператора, ответственного за данную варку, давление и температура в автоклаве) и текущей информации о параметрах варки в текстовом и графическом виде (графики зависимостей давления и температуры от времени) на дисплее компьютера;
- расчет и формирование законов изменения управляемых параметров для реализации автоматического регулирования процессом стерилизации (пастеризации);
- автоматическое управление исполнительными механизмами (клапанами) для точной реализации установленной формулы стерилизации (пастеризации);
- выбор из списка или ввод с панели оператора формулы стерилизации (пастеризации), по которой будет производиться варка, для каждого автоклава;
- ввод, изменение и удаление формул стерилизации (пастеризации);
- формирование архива термобатиграмм каждой варки консервов с возможностью просмотра и распечатки на принтере;
- передача информации с щита управления установленного в цехе на компьютер технолога;
- наблюдение за ходом технологического процесса с компьютера технолога.
В качестве главного управляющего устройства наиболее подходящим вариантом для данных условий является программируемый логический контроллер (ОВЕН ПЛК). Для увеличения его входов и выходов можно применить модули ввода и вывода. На данном устройстве можно построить систему управления любой сложности, а его стоимость незначительно отличается от устройств с гораздо более ограниченными возможностями.
Схема электрическая функциональная рассматриваемой в статье системы регулирования приведена на рисунке 2.
Объектом управления в данной схеме является вертикальный автоклав. Параметры регулирования – температура и давление, взаимосвязаны между собой. Потому в системе предусмотрено два связанных канала управления по температуре и давлению.
Главным управляющим устройством, к которому стекается вся фиксированная информация технологического процесса – является программируемый логический контроллер ПЛК150 (фирма ОВЕН).
В системе происходит измерение температуры в автоклаве с помощью термосопротивления. Информация поступает непосредственно на универсальный вход контроллера.
Кроме температуры внутри автоклава происходит непрерывное измерение рабочего давления при помощи датчика с выходным унифицированным сигналом от 4 до 20 мA. Для исключения аварийной ситуации в режиме охлаждения, когда происходит слив горячей воды и заполнение автоклава холодной водой, в магистраль холодной воды установлен датчик давления, который контролирует необходимый напор воды в магистрали холодного водоснабжения. Если напор воды упадет ниже допустимого, то система выдаёт сигнал для оператора. Оператор в свою очередь закрывает кран, соединяющий автоклав с магистралью холодного водоснабжения, и подключает на данный вход автоклава магистраль с водой из запасного резервуара. Тем самым охлаждение будет продолжаться и не произойдёт уменьшение уровня давления в автоклаве. Цикл работы автоклава продолжится по той же программе. Информация с датчиков давления поступает на унифицированные входа контроллера. По желанию заказчика существует возможность выполнить контроль необходимого давления так же на магистрали подачи пара и воздуха с выполнением системой необходимых действий при аварийных ситуациях.
В качестве модуля управления выходными устройствами выбран модуль выхода управляющий МВУ8 (фирма ОВЕН). Связь между контроллером и модулем расширения выходов МВУ8 осуществляется по промышленному сетевому интерфейсу RS-485.
Для отображения информации техпроцесса непосредственно на объекте (пульте оператора) используется панель оператора ИП320 (фирма ОВЕН). Связь между контроллером и цифровой панелью ИП320 осуществляется так же по сетевому интерфейсу RS-485.
Передача данных и управление с верхнего уровня производится по интерфейсу Ethernet. В качестве SCADA-системы для визуализации, архивирования и управления процессом использована среда программирования CoDeSys (рисунок 3). По желанию заказчика может использоваться любая другая SCADA-система.
Управление каналами регулирования температуры и давления выбрано непрерывное (линейное) для обеспечения нужной точности регулирования – неравномерность температурного поля 2 0С, давления 0,02 МПа. Таким образом, управление исполнительными механизмами производится с МВУ8 непрерывно изменяющимися сигналами от 4 до 20 мA.
В качестве исполнительного механизма выбран мембранный односедельный пневматический клапан с пневмопозиционером (для увеличения точности регулирования). Выбор данного устройства мотивирован его быстротой срабатывания и высокой чувствительностью к управляющему сигналу. Электрические исполнительные механизмы (с электроприводом) в этом отношении значительно проигрывают.
Так как исполнительные механизмы являются пневматическими, то для преобразования стандартного электрического сигнала 4-20 мA в пневматический 0,02-0,1МПа (для управления мембранным исполнительным механизмом) в схеме используются электропневматические преобразователи ЭПП.
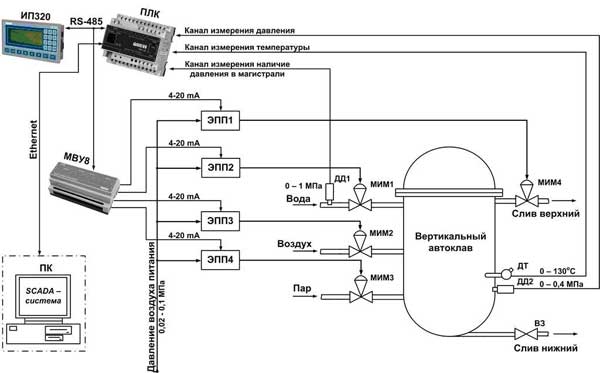
ПК - персональный компьютер; ИП320 - цифровая панель оператора; ПЛК - программируемый логический контроллер; МВУ8 - модуль вывода управляющий; ЭПП1-ЭПП4 - электропневматический позиционер; МИМ1-МИМ4 - клапан с пневматическим мембранным исполнительным механизмом; ВЗ - вентиль запорный; ДТ - датчик температуры; ДД1-ДД2 - датчик давления.
№ | Наименование оборудования | Кол-во |
---|---|---|
1 | Щит системы автоматического управления автоклавом | 1 |
2 | Электропневматический позиционер ЭПП-1 | 4 |
3 | Датчик давления с выходом 4-20 mA | 2 |
4 | Датчик температуры дТС100П | 1 |
5 | Клапан двухседельный с пневматическим исполнительным механизмом мембранного типа | 4 |
Внешний вид щита системы автоматического управления автоклавом приведён на рисунке 4.
В заключение важно отметить, что проекты полностью ориентированы на требования по точности и надёжности, предъявляемые к оборудованию для стерилизации (пастеризации) консервов. Проект требует минимальные расходы на покупку оборудования и его установку, что, в свою очередь, делает его экономически целесообразным к внедрению на производстве. Современное оборудование и новые методы автоматического управления делают разработанную систему надёжной и удобной в эксплуатации. Использование данной системы управления позволит снизить брак продукции и облегчает труд обслуживающего персонала.
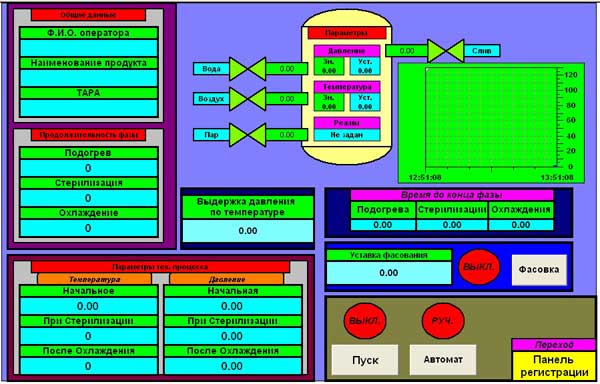
а) Панель управления и мониторинга
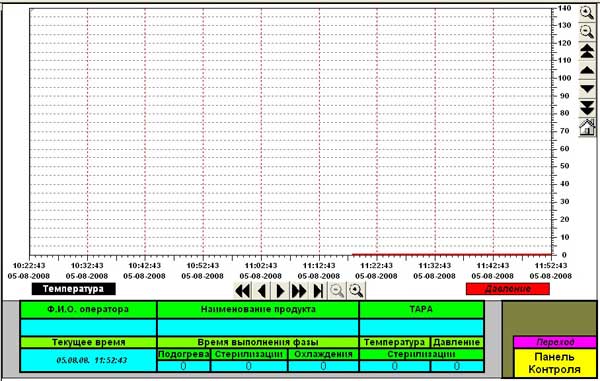
б) Панель регистрации данных
Рис.3. Автоматизированное рабочее место оператора (АРМ)
По всем вопросам, связанным с автоматизацией производства, вы можете обращаться в отдел автоматизации или непосредственно к начальнику отдела Мокрушину Сергею Александровичу.
начальник отдела автоматизации компании «Альфа-Пром»,
аспирант ВятГУ кафедры «Электропривода и автоматизации
промышленных установок»
г.Киров.